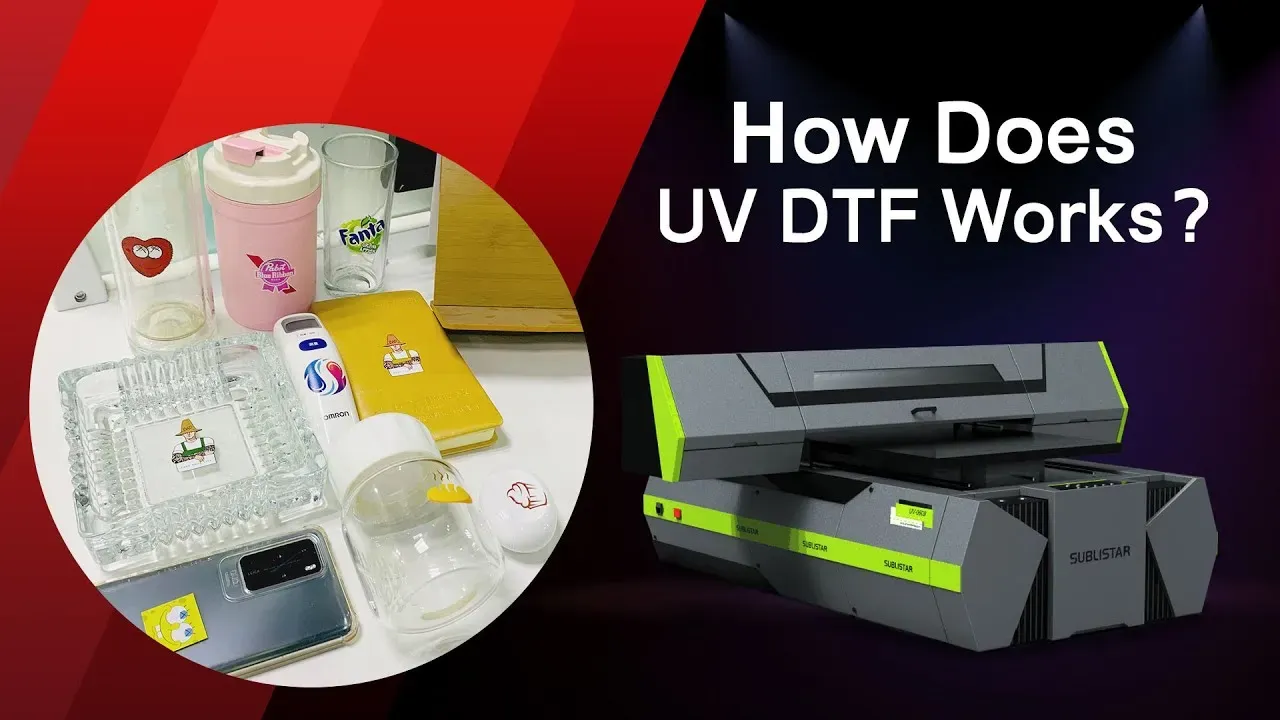
The UV DTF Workflow is revolutionizing the way print shops manage their DTF printing processes, offering remarkable capabilities for vibrant, durable outputs. As digital printing technology evolves, the need to optimize print production becomes paramount for every business aiming to enhance efficiency and satisfaction. In this article, we’ll explore essential UV DTF printing techniques that can elevate your operation, from maintenance best practices to effective workflow strategies. By understanding and implementing DTF workflow optimization, you can achieve not only superior print quality but also streamline your entire production cycle. Engage with our ten expert tips to unlock the full potential of your UV DTF workflow and remain competitive in a fast-paced market.
The process known as Direct-to-Film (DTF) using UV technology is becoming increasingly popular among printing businesses due to its efficiency and quality. This technique involves applying UV light to cure inks as they are printed on films, creating a vibrant, long-lasting output. As printers adopt this innovative method, understanding how to effectively manage the DTF workflow is crucial for maximizing production capabilities and ensuring high standards. From utilizing the best UV printing best practices to exploring various materials, each aspect of the operation plays a pivotal role in achieving optimal results. In this discussion, we will delve deeply into strategies that focus on enhancing your DTF experience through careful workflow management and continuous improvement.
Understanding UV DTF Printing Techniques
UV DTF printing is a revolutionary technique that utilizes ultraviolet light to cure or dry inks as soon as they are printed. This process allows for immediate handling and further processing of printed materials, greatly enhancing workflow efficiency. By familiarizing yourself with the various UV DTF printing techniques, you can select methodologies that optimize your production capabilities while achieving high-quality results. Innovations in this field mean there are constantly evolving best practices to explore, which can significantly improve the effectiveness of your operations.
Key components of successful UV DTF printing include the types of inks used, the speed of your printing machine, and the curing technology employed. By staying abreast of advancements in ink formulations and curing systems, printers can enhance adhesion to a variety of substrates and extend the life of printed products. Therefore, investing time in understanding these UV DTF printing techniques will not only optimize your print production but also set the foundation for ongoing success.
Best Practices for Optimizing Print Production
Optimizing print production is essential, especially in a fast-paced commercial environment like print shops. Incorporating UV printing best practices, such as implementing regular schedules for machine maintenance, can drastically reduce downtime and enhance overall efficiency. Properly maintained printers perform better and produce higher-quality prints, ensuring that your clients receive products that meet or exceed their expectations.
In addition to machine upkeep, utilizing RIP (Raster Image Processor) software can streamline the production workflow by managing print jobs more effectively. This software can automate color management and job scheduling, which minimizes human error and improves turnaround times. Adopting such practices not only enhances production efficiency but also contributes to a more organized work environment, allowing staff to focus on creative aspects and quality assurance.
Strategies for Efficient DTF Printing
Efficiency in DTF printing can be achieved through a myriad of strategic approaches. For instance, fine-tuning your printer settings according to the specific requirements of each job can lead to significant savings in time and resources. By assessing whether you prioritize speed or quality based on project needs, you can adjust resolution and speed settings to ensure optimal output without compromising on detail.
Moreover, testing different materials and substrates before finalizing a print job allows for better resource management. Understanding which materials yield the best print results can minimize waste and enhance overall production efficiency. Implementing these strategies leads to a streamlined printing process that benefits not only the shop’s bottom line but also fosters client satisfaction through timely and high-quality deliverables.
Advanced Techniques for UV Printing Best Practices
To ensure the best outcomes from UV DTF printing, it is essential to stay updated with advanced techniques and practices. Regularly updating ICC color profiles tailored to your substrates can significantly improve color accuracy and overall print quality. As materials and inks evolve, calibrating your machines to match these changes makes a marked difference, reducing the rate of reprints caused by color mismatches or inaccuracies.
Furthermore, the right curing practices should not be overlooked. Ensuring optimal light intensity and proper distance between your UV lamp and substrate can dramatically influence the final quality of your prints. Techniques like conducting daily checks on equipment and replacing aging lamps lead to more reliable and durable prints, solidifying your business’s reputation for high-quality outputs.
DTF Workflow Optimization Techniques
Optimizing your DTF workflow is not just about managing physical aspects of the printing process; it also involves leveraging technology effectively. Incorporating automation for repetitive tasks such as job tracking and resource allocation can dramatically enhance workflow efficiency. By automating these processes, your team can spend more time focusing on intricate tasks that require human oversight, thus improving both productivity and output quality.
Additionally, implementation of a detailed feedback loop from clients can aid in refining your DTF workflow. By regularly soliciting input on print quality and client satisfaction, you can identify areas for improvement and adapt your processes accordingly. This ongoing conversation with clients not only fosters loyalty but also drives your team’s commitment to excellence in crafting quality products.
Importance of Training in UV DTF Workflow
Providing thorough training for staff operating UV DTF printing equipment is essential for achieving an optimized workflow. Well-trained employees who understand the various components and functions of the production process are better equipped to handle challenges as they arise. Regular training that addresses equipment updates, software enhancements, and best practices leads to fewer errors, reduced material waste, and ultimately, an increase in productivity.
In addition, continual education on emerging trends in printing technologies allows your staff to keep pace with industry advancements. By fostering an environment of learning and adaptation, you empower employees to contribute more effectively to the informative aspects of their roles, leading to a more cohesive and well-functioning team. This investment in training not only enhances the capabilities of your workforce but also improves the quality of your final products.
Frequently Asked Questions
What are the best practices for optimizing my UV DTF workflow?
To optimize your UV DTF workflow, focus on maintaining printer cleanliness, using high-quality inks, and ensuring material compatibility. Regularly calibrate color profiles to enhance color accuracy, adjust print settings based on job requirements, and confirm effective curing to guarantee vibrant and durable prints.
How can I improve ink quality in my UV DTF printing process?
Improving ink quality in your UV DTF workflow involves using premium inks that meet manufacturer specifications and adhering to proper storage guidelines. Avoid expired inks to maintain consistency in adhesion and color accuracy, ultimately enhancing the overall quality of your prints.
What role does workflow automation play in efficient DTF printing?
Workflow automation is crucial for efficient DTF printing as it streamlines repetitive tasks such as job scheduling and color management. Utilizing RIP software reduces manual errors, accelerates production timelines, and allows your team to focus on quality control and creative tasks, substantially improving overall productivity.
How do I ensure effective curing in my UV DTF prints?
To ensure effective curing in your UV DTF workflow, regularly check your UV curing unit’s performance, including lamp intensity and proximity to the print surface. Proper curing is vital for ink adhesion and print durability, so maintain regular inspections to prevent under-curing and achieve optimal results.
What training should I provide for employees involved in the UV DTF workflow?
Providing comprehensive training for your employees on UV DTF printing techniques, equipment operation, and the software used is essential. Regular training sessions keep staff updated on best practices and advancements, reducing operational errors and fostering a more efficient and expert workforce.
How can I implement quality control in my UV DTF printing operations?
Implementing a rigorous quality control process in your UV DTF workflow involves establishing clear inspection criteria for printed items before shipment. Documenting any issues allows you to identify trends and continuously improve your process, leading to heightened quality and client satisfaction with final products.
Tip | Description |
---|---|
1. Proper Printer Maintenance | Regular cleaning and maintenance of your UV DTF printer to ensure optimal performance and reduce downtime. |
2. Ink Quality Matters | Utilize high-quality inks and adhere to proper storage practices to maintain print quality. |
3. Material Compatibility | Test various substrates and apply pre-treatment to enhance ink adhesion. |
4. Optimize Color Profiling | Calibrate your printer and develop ICC profiles for consistent color reproduction. |
5. Fine-tune Print Settings | Adjust print settings according to job requirements to improve quality and speed. |
6. Ensure Effective Curing | Check your UV curing unit to ensure proper ink adhesion and durability. |
7. Implement Workflow Automation | Use technology to automate repetitive tasks and enhance efficiency. |
8. Invest in Employee Training | Provide ongoing training for staff to reduce errors and improve operations. |
9. Implement Rigorous Quality Control | Establish a structure for quality inspection to maintain high standards. |
10. Create a Feedback Loop | Engage with clients for feedback to drive continuous improvement. |
Summary
UV DTF Workflow optimization is critical for maximizing print quality and operational efficiency in digital printing. By implementing effective maintenance practices, ensuring high ink quality, and aligning staff training with industry standards, print shops can achieve superior results. Continuous assessment and adaptation of these strategies will not only elevate the quality of prints but also enhance customer satisfaction, thereby fostering business growth. This workflow, when efficiently managed, ensures that businesses stay competitive in the rapidly evolving printing landscape.