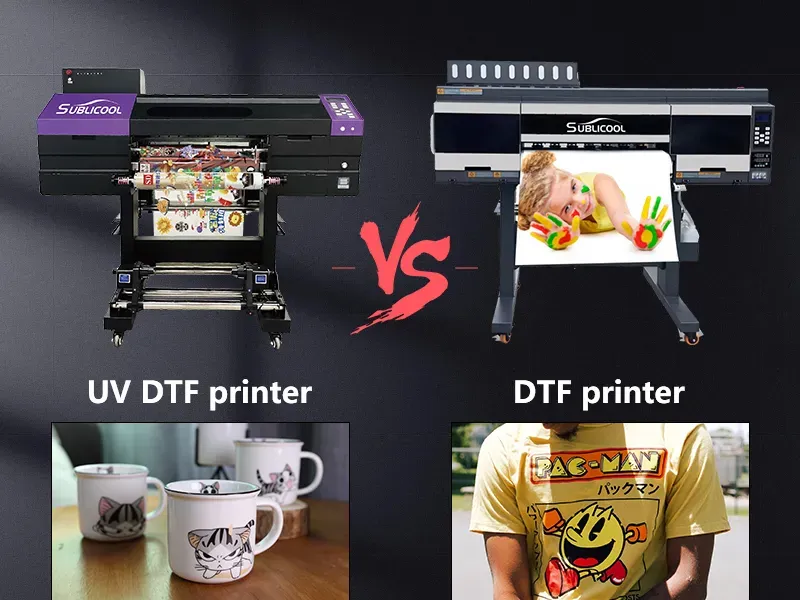
In the dynamic realm of print technology, the comparison of UV DTF versus traditional printing emerges as a crucial discussion for businesses aiming to optimize their printing processes. UV DTF printing revolutionizes the marketplace with its innovative approach, enabling quicker turnaround times and high-quality results across a diverse range of substrates. As brands seek traditional printing advantages alongside modern solutions, the print quality comparison becomes essential in understanding which method best meets their needs. With an emphasis on eco-friendly printing practices, UV DTF’s lower environmental impact makes it a compelling choice in today’s conscientious consumer landscape. As we delve deeper into the intricacies of these printing techniques, it becomes clear that each has unique benefits that could potentially reshape the future of the printing industry.
When exploring the printing landscape, one cannot overlook the distinctions between UV Direct-to-Film printing and conventional printing methods. Often referred to as legacy printing, traditional techniques have long dominated the market, but now face fierce competition from the emergent UV DTF technology. This discussion highlights the benefits of modern printing innovations versus established methods, providing valuable insights for businesses. Furthermore, as the demand for versatile printing options escalates, understanding substrate adaptability plays a pivotal role in selecting the right printing technology. In this article, we will dissect the strengths and weaknesses of these approaches, equipping businesses with the knowledge necessary to make informed decisions.
Understanding UV DTF Printing Technology
UV DTF (Direct-to-Film) printing is a cutting-edge technology that allows for the immediate curing of inks using ultraviolet light. This innovative process enables vibrant colors and detailed designs that are ideal for various substrates, including textiles, wood, plastic, and metals. Unlike traditional methods that require longer drying times, UV DTF ensures that the printed material is ready for handling almost instantly, thus enhancing workflow efficiency. Moreover, this printing technique produces minimal waste, making it a viable option for businesses looking to reduce their environmental impact.
Another key aspect that sets UV DTF apart from other techniques is its substrate versatility. This method can adhere to both porous and non-porous materials without deterioration in print quality. This flexibility allows businesses to expand their product offerings without the need for multiple printers designed for specific tasks. Overall, UV DTF printing represents a significant technological advancement that meets the growing demands for high-quality, customized prints.
Traditional Printing Techniques: A Tried and Tested Approach
Traditional printing encompasses a range of well-established techniques such as offset, screen, and lithographic printing. These methods have been the backbone of the printing industry for decades, offering reliable results that many businesses have come to trust. One of the significant advantages of traditional printing is its cost-effectiveness for large-volume production runs. As print quantities increase, the per-unit cost tends to decrease significantly, making it a preferred choice for bulk orders.
However, traditional printing methods also have their limitations. While they can deliver satisfactory quality, prints often lack the sharpness and vibrancy seen in UV DTF outputs. Additionally, the setup time for traditional prints can be extensive, sometimes resulting in longer production times compared to their UV DTF counterparts. Despite these challenges, traditional methods remain entrenched in the industry for their proven track record and reliability.
Print Quality Comparison: UV DTF vs Traditional Printing
When examining print quality, UV DTF printing clearly sets itself apart from traditional printing methods. One notable advantage of UV DTF is its capacity to produce higher resolution images with enhanced detail. The immediate curing process prevents ink bleeding and color dullness that can occur with traditional printing. This leads to sharper images and a more vibrant color palette, making UV DTF particularly advantageous for businesses looking to produce intricate designs and eye-catching prints.
On the other hand, traditional printing methods may fall short in delivering the same level of detail and color fidelity. While they are effective for many applications, the risk of ink bleed and extended drying times can compromise the final product’s quality. In high-demand environments where visual impact matters, UV DTF offers a superior solution that aligns with contemporary consumer expectations for print aesthetics.
Exploring Eco-Friendly Printing Solutions
In an era where sustainability is paramount, UV DTF has emerged as a more environmentally friendly alternative to traditional printing methods. UV DTF printing typically involves lower emissions of volatile organic compounds (VOCs), which are harmful to both health and the environment. The technology minimizes waste through its efficient ink application process, making it a key player in eco-conscious industries.
Conversely, many traditional printing techniques rely on solvent-based inks that can pose significant environmental challenges. These inks often lead to greater emissions and waste production overall. Businesses that prioritize sustainability can benefit from adopting UV DTF printing not just to enhance their product offerings, but also to fulfill their commitment to eco-friendly practices.
Substrate Versatility in Modern Printing
One of the standout features of UV DTF printing is its unparalleled substrate versatility. UV DTF printing can seamlessly adhere to a wide array of materials—ranging from textiles to metals and plastics—allowing businesses to diversify their product lines without investing in multiple printing rigs. This adaptability opens up numerous market opportunities and caters to various customer needs with ease.
In contrast, traditional printing methods often require specialized printers for different surfaces, constraining a printer’s ability to innovate and expand product offerings. For example, screen printing is generally favored for textiles, while offset printing is utilized for flat and rigid surfaces. This specialization can limit flexibility, making UV DTF a more appealing choice for forward-thinking businesses looking to streamline their operations and capitalize on diverse opportunities.
Cost Analysis: Initial Investment vs. Long-Term Savings
When evaluating the cost implications of UV DTF versus traditional printing, businesses must consider both upfront investments and long-term operational costs. While the initial purchasing price of UV DTF printers can be higher, the rapid production capabilities and reduced setup times often lead to significant savings in labor and material costs over time. This is particularly beneficial for small to medium-sized enterprises aiming to enhance efficiency without sacrificing quality.
Conversely, traditional printing setups usually incur high initial costs and lengthy setup processes, which can deter smaller businesses from utilizing them effectively. Although economies of scale make traditional methods cheaper per unit at high volumes, UV DTF’s flexibility and speed can make it the more economically viable option for varied and short-run production needs. A comprehensive cost analysis will reveal the true value of both methods in meeting specific business requirements.
Frequently Asked Questions
What are the main differences between UV DTF printing and traditional printing?
The main differences between UV DTF printing and traditional printing lie in the printing process and output quality. UV DTF printing uses ultraviolet light to cure inks instantly, resulting in vibrant colors, fast production, and substrate versatility, while traditional printing methods may involve longer drying times, potentially less vivid colors, and limitations on materials.
What advantages does UV DTF printing offer over traditional printing methods?
UV DTF printing offers numerous advantages over traditional printing methods, such as faster production times due to immediate ink curing, high-quality prints with vibrant colors and fine details, and the ability to print on a wide range of substrates, making it a versatile option for various applications.
Is UV DTF printing more eco-friendly than traditional printing methods?
Yes, UV DTF printing is considered more eco-friendly than traditional printing methods. It produces fewer volatile organic compounds (VOCs) and minimizes waste, contributing to a lower carbon footprint, while many traditional printing techniques still rely on solvent-based inks that can be harmful to the environment.
How does print quality in UV DTF compare to that of traditional printing?
Print quality in UV DTF significantly outperforms traditional printing. UV DTF produces sharper images and more vibrant colors thanks to its quick curing process, which preserves the clarity and richness of the print, while traditional printing can suffer from bleeding and dullness.
What types of substrates can be printed on using UV DTF compared to traditional printing?
UV DTF printing can accommodate a wide variety of substrates, including plastics, metals, textiles, and woods, without compromising quality. In contrast, traditional printing methods often have limitations on the types of materials they can effectively print on.
Which printing method is more cost-effective for large production runs: UV DTF or traditional printing?
For large production runs, traditional printing methods are often more cost-effective due to lower per-unit costs as quantities increase. However, UV DTF’s faster turnaround times and flexibility can offset these costs for smaller to medium-sized businesses, especially those that print on demand.
Key Features of UV DTF Printing | Key Features of Traditional Printing |
---|---|
Instant curing of inks using ultraviolet light results in bright colors and detailed prints on various substrates such as textiles and plastics. | Includes methods like screen printing and offset printing, which rely on older techniques and longer ink drying times, impacting turnaround. |
Offers vibrant colors and sharp images due to immediate curing, enhancing clarity and richness in prints. | While traditional methods can produce good quality, issues like bleeding or prolonged dullness can arise under certain conditions. |
Allows for faster production rates due to quick curing, making it suitable for businesses that need rapid results. | More cost-effective for large-scale runs, with lower per-unit costs as quantities increase, but less efficient for small orders. |
Can print on a wide range of materials without compromising quality, offering versatility in products. | Specialized printing methods are often limited to certain materials, which may not be suitable for diverse product ranges. |
Generates lower VOC emissions, contributing to an environmentally friendly approach to printing. | Traditional inks may contain harmful solvents, resulting in higher emissions and a larger environmental footprint. |
Although initial costs are higher, UV DTF’s speed and efficiency can lead to cost savings in the long run, especially for smaller operations. | Higher setup costs can make traditional printing less economical for smaller print runs, despite being cheaper for bulk orders. |
Summary
In examining UV DTF vs Traditional Printing, it is clear that UV DTF technology presents modern businesses with remarkable advantages in print quality and efficiency. This innovative method allows for instant curing of inks, resulting in vibrant and detailed prints that cater to a range of substrates. While traditional printing methods still serve well for large-scale projects, their limitations in speed and environmental impact cannot be overlooked. For businesses looking to optimize their printing processes, understanding the unique benefits and applications of each method is essential for making informed decisions that align with their operational goals.