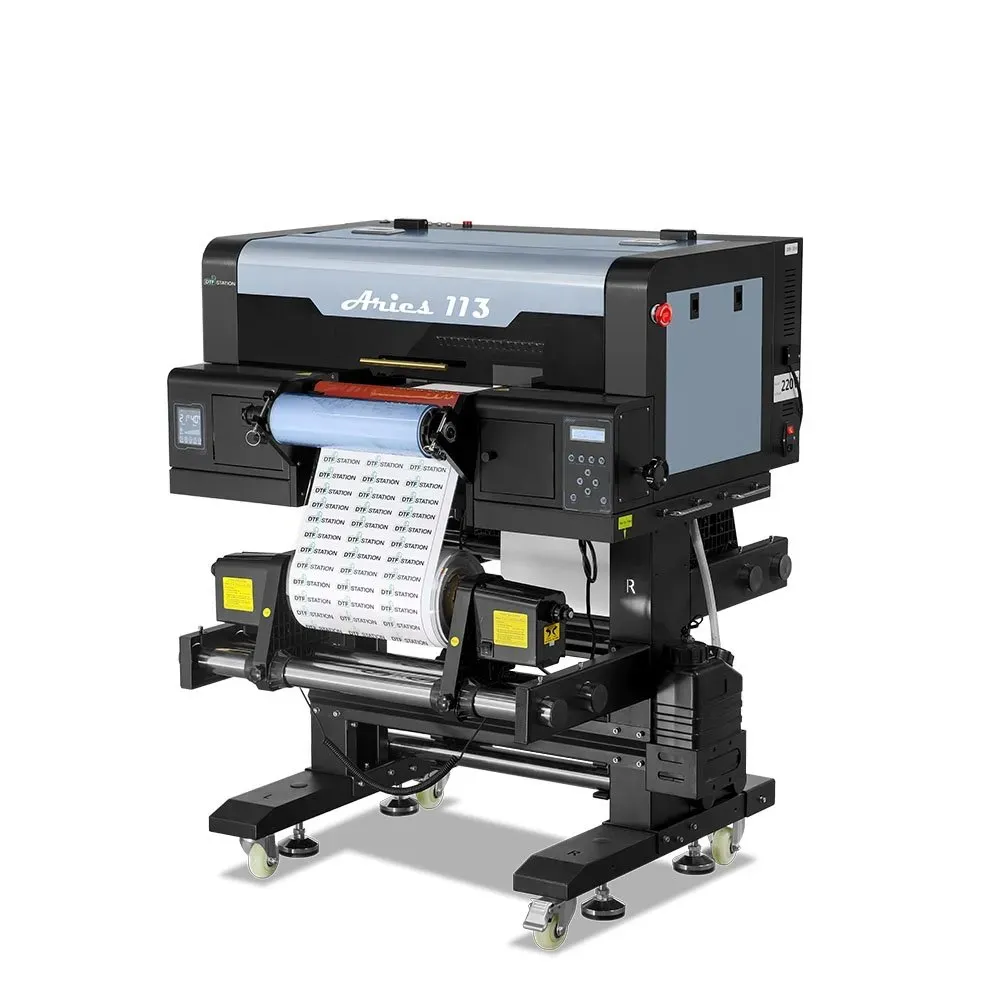
In the dynamic realm of modern printing, **UV Direct-to-Film (DTF)** printing stands out as an innovative solution that blends cutting-edge technology with exceptional design capabilities. This sophisticated printing method incorporates advanced UV printing techniques, enabling vibrant and durable prints on various surfaces. With the demand for high-quality, custom printing escalating, UV DTF printing has emerged as a preferred choice for manufacturers seeking to deliver remarkable results. By harnessing the advantages of sustainable printing solutions, this technology not only ensures longevity but also resonates with eco-conscious consumers. In this guide, we will delve into the essentials of mastering UV DTF, empowering you to achieve stunning results every time.
Known alternatively as UV film printing, this technique revolutionizes the way products are customized and branded. By combining the qualities of ultraviolet and direct-to-film processes, it allows for precision printing that meets the diverse needs of various industries. This method’s unique approach ensures that prints are not only visually striking but also resilient, making it ideal for both fashion and promotional items. As the printing technology continues to evolve, it opens new avenues for creativity and innovation. In this exploration of UV DTF, we will uncover its potential and provide a comprehensive guide for enthusiasts and professionals alike.
Introduction to UV DTF Printing
UV Direct-to-Film (DTF) printing has emerged as a transformative method in the world of custom printing. By combining the principles of UV printing with innovative DTF techniques, this technology allows for stunning designs that can easily be transferred onto a variety of materials. It offers a unique solution for businesses seeking to create high-quality merchandise, including garments and promotional products. The transition to UV DTF means quicker turnaround times, which is essential in today’s fast-paced market.
Moreover, UV DTF printing promotes sustainability through its efficient use of inks and the minimal waste generated during the process. Unlike traditional printing methods that can have high emissions, UV DTF reduces environmental impact, making it an attractive option for companies committed to sustainable printing solutions. As businesses increasingly seek methods that align with eco-conscious consumer preferences, UV DTF represents a forward-thinking approach to modern printing technology.
Key Benefits of UV DTF Technology
One of the standout benefits of UV DTF technology is its ability to produce vivid colors and intricate details that are often challenging to achieve with other printing methods. The UV curable inks cure instantly under ultraviolet light, ensuring that designs are vibrant and durable while reducing drying times markedly. This characteristic makes UV DTF an ideal choice for creating stunning visuals on textiles, plastic, and other substrates, capturing the attention of the target audience.
Additionally, UV DTF printing enhances the durability of prints, making them resistant to fading, scratching, and washing, thereby increasing the lifespan of the printed designs. This durability is a significant advantage for businesses that want to ensure their products remain attractive even after extensive use. By leveraging UV printing techniques alongside DTF processes, companies can deliver long-lasting custom prints that elevate their brand image and satisfy customer expectations.
Essential Equipment for UV DTF Printing
To successfully embark on a UV DTF printing journey, investing in high-quality equipment is paramount. A reliable UV printer that can handle DTF functionalities is essential for achieving optimum results. The choice of printer can significantly influence print quality, so it’s advisable to opt for models with high resolution and sophisticated color management features. Ensuring that your printer supports the specific inks you intend to use is also crucial for consistency in results.
In addition to the printer, high-quality transfer films are a necessity when working with UV DTF technology. These films should be compatible with UV curable inks to ensure adhesion and transfer efficacy. A UV curing lamp is another vital piece of equipment required to solidify the inks immediately after printing. This curing step is critical, as it not only enhances print durability but also eliminates the drying period that can slow down production workflows.
Design Preparation for UV DTF Printing
The preparation phase is key to successful UV DTF printing, as it sets the foundation for the quality of the finished product. Utilizing sophisticated graphic design software like Adobe Illustrator or CorelDRAW helps in crafting designs that resonate with the target audience. It’s essential to ensure the design files meet the printing specifications and include high resolution (at least 300 DPI) to maintain clarity and attraction both up close and at a distance.
Furthermore, choosing appropriate color profiles optimized for UV printing will ensure accurate color reproduction. This step is critical as certain colors may look different when printed than they do on-screen. Using a color management system can aid in achieving consistent results across various media, which is a key element of any successful custom printing venture.
Step-By-Step Printing Process of UV DTF
The actual printing process for UV DTF starts once your designs are perfectly prepared and ready for transfer. Begin by carefully loading the transfer film into your UV printer, ensuring it’s aligned precisely as per the specifications set out in the printer’s user manual. Correct alignment is crucial as any inconsistencies could interrupt the printing process and negatively affect the final outcome.
Once the film is loaded, configuring the printer settings appropriately comes next. Adjusting parameters such as ink density and layer settings according to manufacturer recommendations will ensure that the output matches your vision. Initiating the print job should be accompanied by monitoring it closely, as vigilance during this phase can help identify any potential issues before they escalate into more significant problems.
Post-Processing Techniques for Enhanced Durability
After the printing and curing processes are complete, conducting a thorough quality assessment is the next step in ensuring your product meets high standards. Inspect the final prints closely for any imperfections, which could indicate issues with the curing process or ink adhesion. This inspection process is essential not only for aesthetic reasons but also to meet the durability requirements specified by clients.
For items that will endure heavy use, an additional post-curing step may be beneficial. This process can further solidify the inks and enhance their resilience against wear and tear, which is especially important for products like clothing or accessories. By adopting these post-processing techniques, businesses can assure clients of the quality and durability of their UV DTF printed products.
Frequently Asked Questions
What is UV DTF printing and how does it differ from traditional printing methods?
UV DTF printing, or Ultraviolet Direct-to-Film printing, is a modern printing technology that combines UV printing techniques with the flexibility of DTF methods. Unlike traditional printing, which may require drying time, UV DTF printing uses UV light to instantly cure specially formulated inks on transfer films. This results in vibrant, durable prints suitable for various surfaces, making it ideal for custom merchandise and promotional products.
What equipment do I need for UV Direct-to-Film printing?
To successfully engage in UV Direct-to-Film (DTF) printing, you will need key equipment such as a high-quality UV printer capable of DTF functionalities, compatible transfer films for effective ink adhesion, and a UV curing lamp to set the inks immediately after printing. This combination ensures optimal print quality and durability in your custom printing projects.
Can UV DTF printing be used for sustainable printing solutions?
Yes, UV DTF printing is considered a sustainable printing solution as it typically involves lower emissions compared to traditional printing methods. The curing process uses UV light, which can reduce the environmental impact by minimizing volatile organic compounds (VOCs). Many manufacturers are adopting UV DTF technology to align with eco-friendly practices while producing high-quality custom prints.
What are the key advantages of using UV printing techniques in DTF printing?
The key advantages of utilizing UV printing techniques in DTF printing include enhanced color vibrancy, fine detail capabilities, and immediate curing times. This technology allows for durable prints that can withstand wear and tear, making it perfect for custom garments and promotional items. Moreover, UV DTF printing supports a diverse range of substrates, expanding the possibilities for creative applications.
How do I prepare my designs for UV DTF printing?
To prepare your designs for UV DTF printing, start by using graphic design software to ensure high resolution, ideally 300 DPI, for sharpness. Additionally, applying color profiles optimized for UV printing is crucial for maintaining color accuracy and vibrancy in the final print. Proper design preparation is key to achieving stunning results.
What are some recent developments in UV DTF technology?
Recent developments in UV DTF technology include new ink formulations that enhance print vibrancy and durability while reducing curing times. These innovations boost workflow efficiency and meet the rising market demands for custom printing solutions. Additionally, the trend towards sustainable printing practices has prompted many companies to adopt UV DTF technology, reflecting changing consumer preferences towards eco-friendly options.
Section | Key Points |
---|---|
Introduction | Overview of UV DTF printing as a blend of UV printing and DTF methods, ideal for vibrant and durable prints. |
Understanding UV DTF Technology | Integration of film printing and UV curing allows for quick handling and high-quality, long-lasting prints. |
Equipment and Materials | Use a reliable UV printer, high-quality transfer films, and a UV curing lamp for best results. |
Design Preparation | Create designs in high resolution (300 DPI) and use optimized color profiles. |
Printing Process | Ensure proper film loading, printer settings, and monitor the print job for quality. |
Curing the Print | Use UV light for curing as per ink guidelines to solidify prints effectively. |
Transferring the Print | Utilize a heat press, adjust settings as needed, and allow cooling for quality transfer. |
Post-Processing | Inspect the final product for quality and consider additional curing if necessary. |
Recent Developments | Monitor innovations and market trends shaping the future of UV DTF printing. |
Recommended Resources | Explore available guides and articles to deepen your understanding of UV DTF printing. |
Summary
UV DTF printing has emerged as a revolutionary technique that transforms the printing landscape, allowing for exceptional outcomes with vibrant colors and exceptional durability. By following a systematic approach, from understanding the technology and preparing designs to mastering the printing and transfer processes, users can achieve stunning outputs. As technology advances, staying abreast of new developments and best practices in UV DTF printing not only enhances one’s skills but also ensures that they remain competitive in a growing market. With the right equipment, materials, and knowledge, UV DTF printing can become a powerful tool for creating remarkable custom products that captivate audiences.