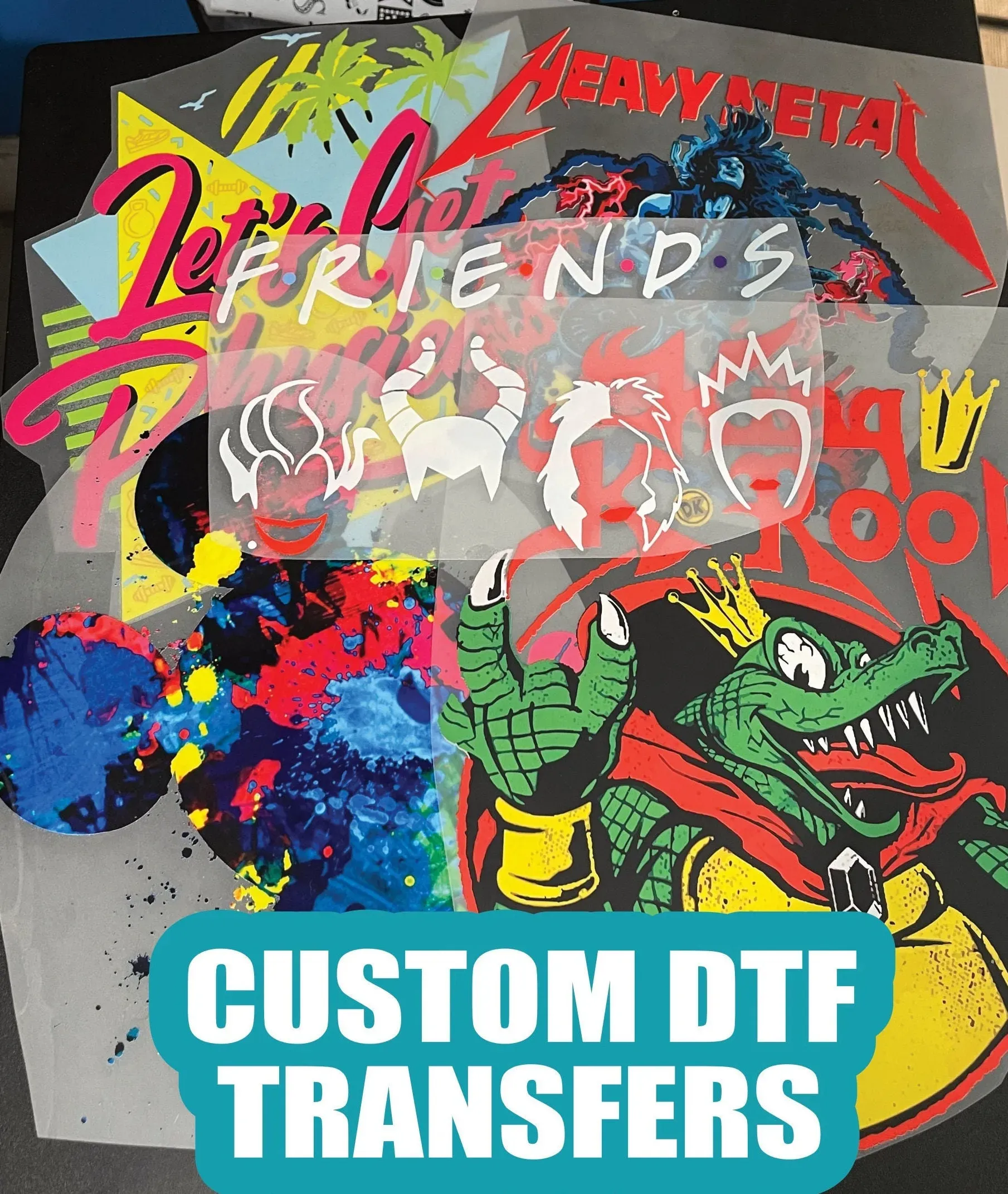
DTF transfers, or Direct to Film transfers, have revolutionized the landscape of textile printing, allowing creators to produce vibrant, high-quality images on fabric with remarkable ease. As this innovative printing method gains traction, it’s crucial for users to be aware of common DTF printing mistakes that can detract from the final product’s quality. From improper print settings to overlooked fabric compatibility, each misstep can lead to disappointing results that undermine the potential of DTF transfer quality. In this guide, we will highlight the best practices for DTF to ensure your projects flourish while avoiding the pitfalls associated with Direct to Film printing issues. Join us as we delve into the top 5 mistakes to avoid, paving the way for successful and visually stunning transfer projects.
Direct to Film printing, often referred to simply as DTF printing, has emerged as a go-to choice for innovative textile enthusiasts and professional printers alike. This technique enables the transfer of intricate designs onto various fabric types, but it is not without its challenges. Understanding the intricacies of DTF transfers, including common issues such as inadequate curing and the effects of fabric compatibility, is essential for achieving optimal results. By focusing on effective practices and troubleshooting potential problems, printers can elevate their work and ensure that each transfer meets their high standards. In this article, we will explore the critical aspects of navigating the DTF printing process and discuss how to avoid common mistakes that may compromise the integrity of your prints.
Understanding DTF Printing Mistakes
DTF printing, or Direct to Film printing, is a technique that has revolutionized the textile printing landscape, providing exceptional quality and versatility. However, to achieve superior results, one must be aware of the common DTF printing mistakes. Failing to recognize these pitfalls can lead to not only wasted materials but also disappointing outcomes that can affect your brand’s reputation in the long run. Therefore, understanding these mistakes is pivotal for any serious printer looking to deliver top-notch products.
By identifying issues such as improper print settings and inadequate curing, printers can proactively take steps to avoid them. Common pitfalls include neglect in setting the printer to the right resolution or incorrect alignment of the images being printed. These errors not only diminish DTF transfer quality but can result in extra costs and time delays that can be detrimental, especially for businesses with tight deadlines.
Troubleshooting Direct to Film Printing Issues
Direct to Film printing issues can arise from various factors, including equipment malfunction, improper maintenance, and the use of subpar materials. One of the most effective solutions is to maintain your printing equipment regularly, ensuring that everything from print heads to inks is in optimal condition. Doing so minimizes print defects and ensures that the outcome meets high-quality standards.
Furthermore, it’s essential to be familiar with common troubleshooting techniques. If certain colors are not adhering correctly to the fabric, it may indicate that the materials you’re using are incompatible with DTF methods. Regularly testing various substrates can help identify which fabrics yield the best results during the printing process.
Best Practices for DTF Transfers
Implementing best practices for DTF transfers is crucial to achieving outstanding results. This includes not only adhering to proper print settings and curing times but also investing in high-quality DTF films and inks. Quality materials are vital for vibrant and durable results, which can directly influence customer satisfaction and repeat business.
In addition, experimenting with the combinations of settings and materials will lead to a deeper understanding of the process. Keeping detailed records of successful print settings and materials can serve as a valuable reference for future projects. These best practices not only simplify the DTF printing experience but also elevate the overall quality of produced items.
Ensuring DTF Transfer Quality
Achieving high-level DTF transfer quality involves several key components, including material compatibility, precise printing techniques, and effective curing processes. Each aspect plays a significant role in how well the design adheres to the fabric and maintains its integrity over time. This is particularly important for businesses focused on delivering reliable and high-quality prints.
To enhance DTF transfer quality, it’s advisable to conduct fabric compatibility tests, ensuring that the selected materials can handle the DTF process without compromising results. Additionally, investing time in learning and applying proper printing techniques will help maintain the integrity of the image while ensuring it can withstand washes and general wear.
Fabric Compatibility with DTF Printing
Fabric compatibility with DTF printing is a critical factor that determines the success of your projects. While DTF transfers work best with polyester and polyester blends, understanding the nuances of different fabrics can greatly enhance your printing results. Many printers make the mistake of assuming that any fabric will work without testing, leading to issues with adhesion and print quality.
To avoid these complications, it’s vital to perform thorough checks on the fabric you intend to use for DTF transfers. Consider factors such as the fabric’s composition, texture, and color. Conducting small test runs on various fabrics can help you determine the best matches for DTF printing, ensuring that your final products deliver the quality and durability customers expect.
The Importance of Pre-Treatment in DTF Transfers
Pre-treatment is a step often overlooked in the DTF transfer process but is essential for enhancing adhesion and overall transfer quality. Applying a pre-treatment solution properly prepares the fabric for the DTF transfer, increasing the bond between the film and substrate, which directly affects how the transfer performs during washing and wear.
Without proper pre-treatment, users may face challenges such as incomplete transfers or lifting edges, leading to dissatisfaction and wasted resources. Therefore, investing time in mastering the pre-treatment process ensures that you achieve optimal results with your DTF transfers, giving you a competitive edge in the market.
Frequently Asked Questions
What are common DTF printing mistakes to avoid?
Common DTF printing mistakes include improper print settings, using low-quality materials, inadequate curing, neglecting fabric compatibility, and skipping pre-treatment. These pitfalls can lead to poor DTF transfer quality and wasted materials. Always ensure your printer settings are optimized, use high-quality films and inks, adhere to curing guidelines, check fabric compatibility, and apply pre-treatment when necessary to achieve the best results.
How can I improve DTF transfer quality?
To improve DTF transfer quality, focus on using high-resolution settings during printing, select quality materials, ensure proper curing times and temperatures, and verify fabric compatibility. Additionally, applying pre-treatment can enhance adherence to the fabric. Following these best practices will significantly elevate the quality of your DTF transfers.
What are the best practices for DTF transfers?
Best practices for DTF transfers include carefully adjusting print settings to ensure high resolution, sourcing high-quality transfer films and inks, curing transfers properly, checking the compatibility of fabrics, and applying pre-treatment when necessary. Implementing these guidelines will help avoid common DTF printing mistakes and improve the overall outcome of your projects.
What kind of fabrics work well with DTF transfers?
Fabrics that work best with DTF transfers include polyester and polyester blends. These materials tend to adhere well during the transfer process. Cotton can also be used, but it often requires a pre-treatment step to ensure proper adhesion and DTF transfer quality. Always test different fabrics to find the best compatibility for your specific projects.
What are direct to film printing issues I might encounter?
Direct to Film printing issues can include poor print quality due to incorrect printer settings, adhesion problems caused by using incompatible fabrics, and transfers lifting or peeling due to inadequate curing. To mitigate these issues, ensure that all necessary preparation steps are followed, including proper print resolution, curing, and material compatibility.
How important is pre-treatment for DTF transfers?
Pre-treatment is crucial for achieving superior DTF transfer quality, particularly when printing on fabrics like cotton. It prepares the fabric for better adhesion, preventing issues like incomplete transfers or lifting. Skipping this step can result in unsatisfactory outcomes, so always assess whether pre-treatment is necessary for your specific transfer projects.
Mistake | Description | Tip |
---|---|---|
Improper Print Settings | Failure to adjust print settings can lead to poor-quality transfers. | Always double-check printer settings before printing. |
Using Low-Quality Materials | Subpar materials can cause transfers to peel or not adhere properly. | Source materials from reputable suppliers and test samples first. |
Inadequate Curing | Rushing curing leads to poor adhesion and peeling. | Follow recommended curing times and temperatures. |
Neglecting Fabric Compatibility | Using inappropriate fabrics affects transfer quality. | Check fabric compatibility prior to printing. |
Skipping Pre-Treatment | Skipping pre-treatment can cause ineffective transfers. | Apply pre-treatment solutions on suitable fabrics before printing. |
Summary
DTF Transfers are an innovative solution in textile printing, yet many face challenges that can affect the final output. To achieve optimal results, it is essential to avoid these five critical mistakes: setting incorrect print configurations, choosing low-quality materials, hasty curing processes, overlooking fabric compatibility, and neglecting pre-treatment protocols. By addressing these issues diligently, printers can realize the full potential of DTF Transfers and produce high-quality, durable prints that leave a lasting impression.