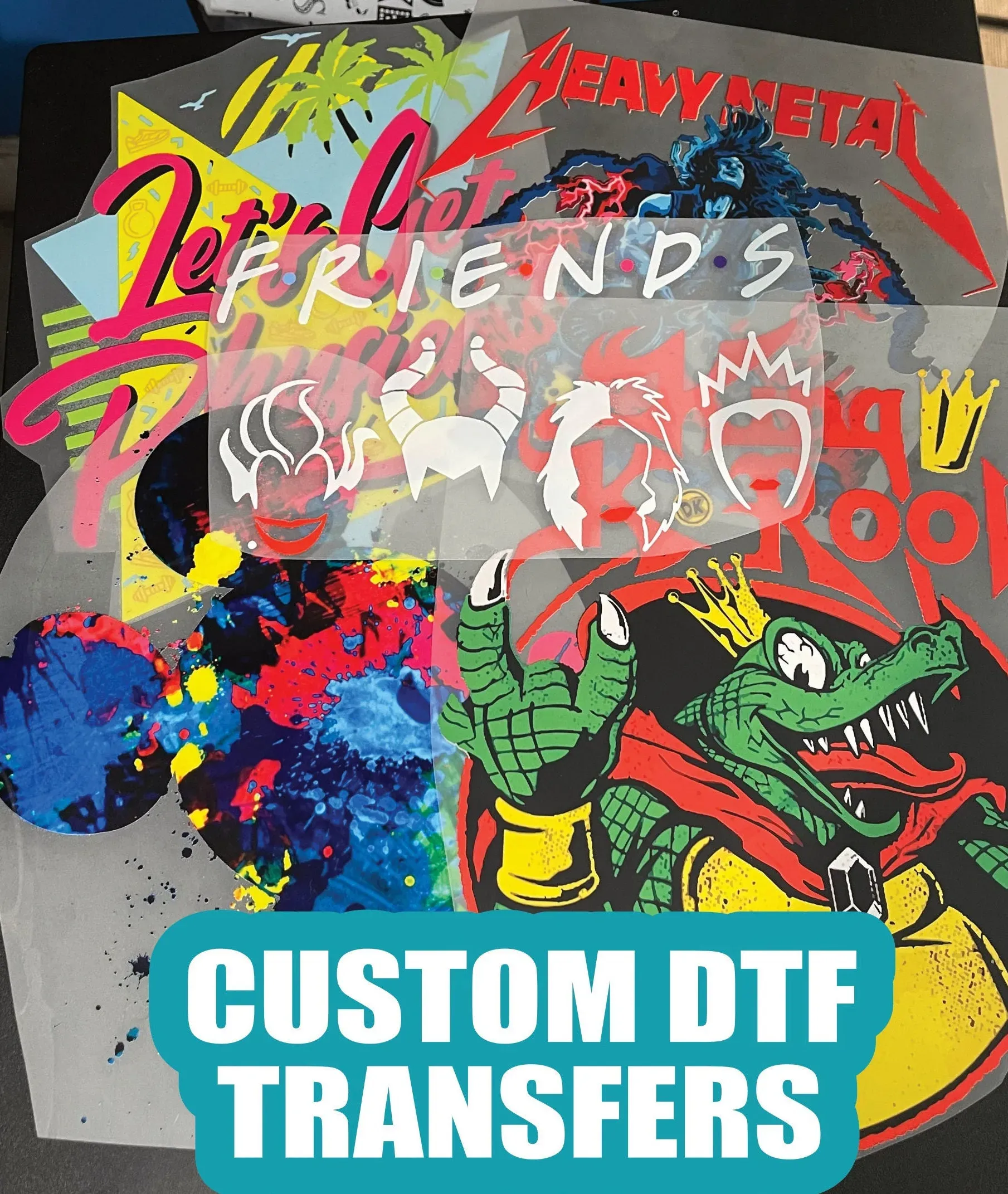
DTF transfers, or Direct-to-Film transfers, are taking the garment printing world by storm, offering a vibrant and versatile solution for transferring intricate designs onto various fabrics. As this innovative printing method grows in popularity, so too do the challenges that can arise during the process. Whether you’re a beginner or a seasoned pro, understanding common mistakes associated with DTF printing errors is crucial for achieving pristine results. In this guide, we will delve into essential tips for DTF printing that can help you avoid pitfalls, such as improper artwork preparation and misconfigured heat settings. By mastering these practices, you can unlock the full potential of DTF transfers to deliver high-quality prints that wow your clients and elevate your offerings.
Also known as Direct-to-Film printing, the technique of DTF transfers allows for high-quality, detailed designs to be effortlessly transferred onto a wide array of textiles. This modern method has opened new avenues for customization in apparel, but it comes with its own set of challenges that require attention to detail. Understanding the nuances of material compatibility, heat application, and adhesive usage is paramount for eliminating common mistakes that can mar your printed products. By implementing best practices tailored for DTF printing, you pave the way for successful projects that meet clients’ expectations. Embracing these techniques positions you at the forefront of the garment printing industry, ready to tackle any design challenge.
The Importance of High-Quality Artwork in DTF Transfers
When it comes to Direct-to-Film (DTF) transfers, the artwork serves as the backbone of the printing process. Ensuring that your images are of high quality is not just an aesthetic choice; it determines the clarity and vibrance of the final product. Low-resolution images can result in pixelation during printing, which adversely affects the impression you want to make. To achieve optimal results, always use artwork with a resolution of at least 300 DPI. This guarantees that your prints will be sharp and visually appealing, thus enhancing customer satisfaction.
Moreover, preparing your artwork with the correct dimensions and color profiles is crucial. Most DTF printers operate best with RGB settings rather than CMYK color formats. By correctly adjusting your files ahead of time, you avoid the risk of muted colors that may occur during printing. Taking these simple yet effective steps ensures your designs will maintain their intended vibrancy and intricacy, significantly improving the overall quality of the DTF transfer.
Choosing the Right Materials for DTF Printing Success
Selecting compatible materials is essential to achieving high-quality DTF transfers. Not all fabrics will produce satisfactory results with this particular printing method. Suitable choices include cotton, poly-blend fabrics, and certain synthetic materials designed to accept heat transfer applications. When using inappropriate substrates, such as stretchy or coated fabrics, you risk poor adhesion and premature wear, leading to a negative outcome for both the print and your reputation.
It’s wise to conduct preliminary material tests to ensure compatibility before engaging in full-scale production. This involves printing samples on new materials and observing how well the DTF transfer adheres and whether the colors appear true to design. Understanding which materials work best for your projects allows you to refine your process, resulting in a more professional finish and greater customer trust in your products.
Heat Press Settings and Their Impact on DTF Transfers
The effectiveness of DTF printing greatly depends on the accuracy of your heat press settings. Many commonly encountered problems stem from incorrect pressure, temperature, or timing during the transfer process. It is pivotal to consult the manufacturer’s recommendations for heat settings that are tailored to the specific materials being used in your project. A miscalibrated heat press can lead to failures such as poor adhesion, burning of the film, or incomplete transfers.
Additionally, implementing a systematic approach to adjusting your heat settings can prevent any costly mistakes. Performing trial runs with varying settings can help you identify the most effective conditions for a specific job. By establishing these best practices for your heat press use, you can maintain the integrity of your DTF transfers, ensuring they remain as durable and vibrant as intended.
Essential Tips for Adhesive Powder Application in DTF Printing
Proper application of adhesive powder is a critical step that can make or break your DTF printing results. Both the over-application and under-application of the powder can lead to significant transfer issues. Ensuring a uniform and appropriate amount of adhesive will safeguard against many common printing errors. Excess powder may create a rough texture after curing, while too little adhesive can result in weak bonding, causing the print to lift or fray with time.
Utilizing automated systems can enhance the consistency and efficiency of adhesive application. If manually applying powder, consider using tools that help distribute it evenly across your prints. Following precise techniques ensures that each DTF transfer adheres correctly to the desired substrate, ultimately enhancing the longevity and quality of your finished products.
Post-Print Care: Preserving the Quality of DTF Transfers
Once your DTF transfers are completed, post-print care is an often-overlooked aspect that significantly impacts product longevity. Proper washing and care instructions must be followed to maintain the vibrancy and integrity of the prints. Using cold water, selecting gentle cycles, and steering clear of harsh detergents can vastly improve the durability of your DTF transfers, keeping them looking fresh even after multiple washes.
Establishing a clear set of care instructions for your clients can also prevent potential dissatisfaction stemming from improper maintenance. Providing guidelines ensures that they understand how to best care for their products, thus reinforcing your brand’s commitment to quality. By investing time in post-print care education, you will encourage pride in ownership of your printed items and foster repeat business.
Implementing Quality Control for Flawless DTF Transfers
Quality control plays a crucial role in ensuring that your DTF printing meets acceptable standards. Neglecting this step can lead to inconsistencies that can damage your reputation and customer satisfaction rates. Establishing a routine for inspecting your transfers before shipping is vital. This can involve checking for issues such as print clarity, color consistency, and alignment, safeguarding your clients from receiving inferior products.
Incorporating a checklist or a standardized procedure for quality assurance can streamline this process, helping to catch any potential errors early on. Regularly assessing the condition of your prints allows you to maintain a high standard of output, enhancing overall client trust in your services. By emphasizing quality control, you showcase your dedication to excellence in DTF printing, encouraging customer loyalty and word-of-mouth recommendations.
Frequently Asked Questions
What are common mistakes to avoid when using DTF transfers?
Common mistakes when using DTF transfers include improper artwork preparation, such as using low-resolution images and incorrect color profiles. Other errors include selecting incompatible materials, setting incorrect heat press settings, poor adhesive application, neglecting post-print care, and lacking quality control. By addressing these pitfalls, you can achieve higher quality DTF prints.
How can I prepare artwork correctly for DTF transfers?
To prepare artwork for DTF transfers, ensure you use high-resolution images of at least 300 DPI and set appropriate dimensions. Use the RGB color space for your designs, as most DTF printers perform better with this profile. Proper preparation is crucial to avoid pixelation and muted colors in your final prints.
What tips can enhance DTF printing success?
To enhance DTF printing success, follow these tips: ensure the use of compatible fabrics like cotton or poly-blends, set accurate heat press settings according to the manufacturer’s guidelines, apply adhesives evenly, and adhere to proper post-care instructions for washing and maintenance. Regular quality checks can also help maintain high printing standards.
What materials work best with DTF transfers?
The best materials for DTF transfers include cotton, polyester blends, and some synthetic fabrics. Avoid using stretchy materials or those with heat-sensitive coatings, as they may lead to print damage or poor adhesion. Always test a small piece before mass printing on new substrates.
What are the best practices for applying adhesive in DTF transfers?
For best practices in applying adhesive during DTF transfers, ensure an even and correct amount of powder is used. Too much adhesive can lead to a rough texture, while too little may cause poor bonding. Utilize automated systems for consistent application or develop refined manual techniques to control application precision.
What should I do for post-print care of DTF transfers?
For post-print care of DTF transfers, follow washing instructions provided by the manufacturer. This typically includes using cold water, gentle wash cycles, and avoiding bleach. Proper care after printing will help maintain the vivid colors and integrity of your DTF prints over time.
Mistake | Description |
---|---|
Improper Artwork Preparation | Using low-resolution images, incorrect dimensions, or unsuitable color profiles can negatively affect print quality. Always use high-resolution images (300 DPI or above) and set files to RGB color profiles for optimal results. |
Choosing Incompatible Materials | Not all fabrics are suitable for DTF transfers. Use compatible fabrics like cotton, poly-blends, and synthetics to avoid issues with adhesion and print quality. |
Setting Incorrect Heat Press Settings | Improper settings for pressure, temperature, and time can affect adhesion. Always follow manufacturer guidelines for the specific materials being used. |
Improper Powder and Adhesive Application | Over or under-applying adhesive can lead to transfer issues. Ensure uniform distribution of adhesive for best results. |
Skipping Post-Print Care | Neglecting post-print care can damage prints. Follow care instructions like cold washes and avoid bleach to maintain print integrity. |
Lack of Quality Control | Neglecting quality checks can lead to unsatisfied customers. Regular inspections for color consistency and clarity are essential for quality assurance. |
Summary
DTF transfers represent a groundbreaking advancement in garment printing, allowing for bold and intricate designs. To achieve the best outcomes with DTF transfers, it’s vital to avoid common mistakes such as improper artwork preparation, using incompatible materials, and neglecting quality control practices. By focusing on high-resolution artwork, selecting the right substrates, and ensuring consistency in printing settings and post-care routines, you can significantly enhance the quality of your prints. Adopting these best practices not only elevates the professionalism of your work but also satisfies customer expectations. Embrace the nuances of DTF transfers to deliver stunning printed garments that stand out in the market.