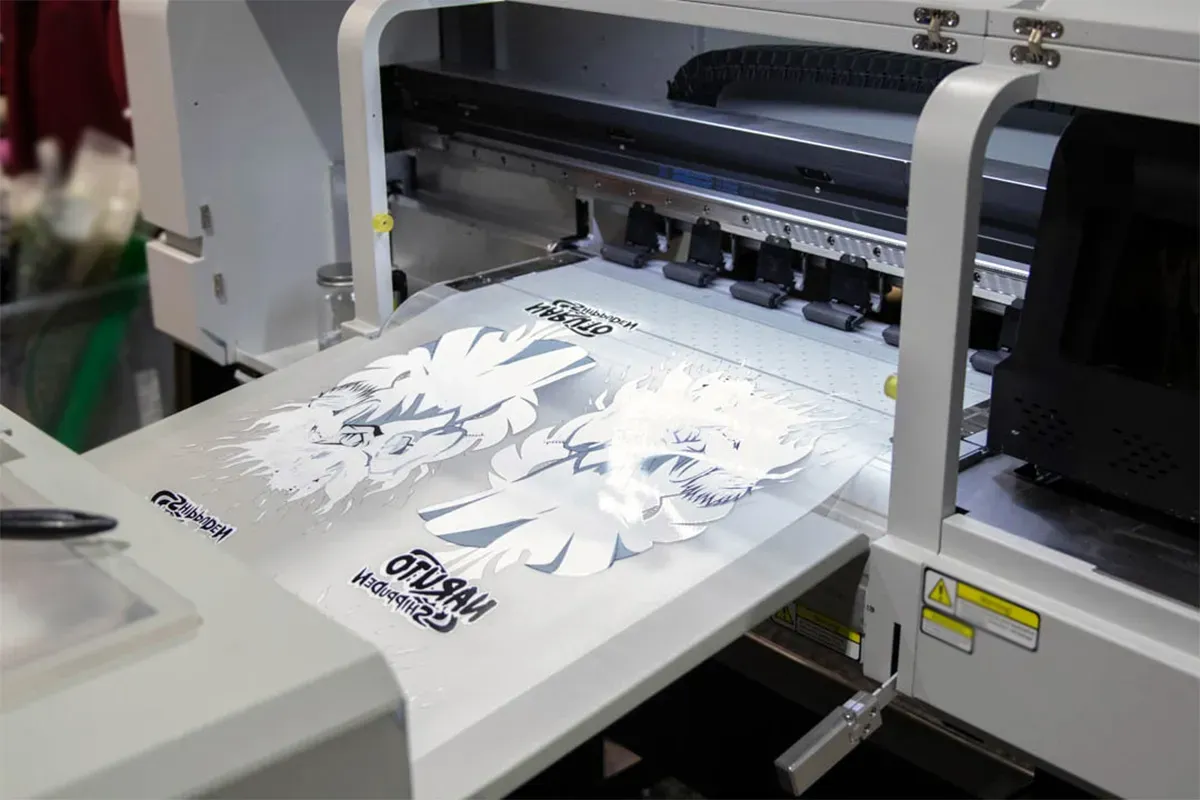
DTF printing efficiency is crucial for businesses that aim to boost productivity while ensuring stunning print quality. This innovative technology has transformed the process of transferring designs onto fabrics, delivering vibrant colors and exceptional durability. However, achieving impressive results requires more than just top-tier equipment; it necessitates the strategic integration of DTF printing tools and best DTF printing techniques. By focusing on efficient DTF processes, businesses can significantly reduce waste and costs associated with printing. In this guide, we will delve into practical strategies to optimize your DTF printing efficiency, helping you enhance your operational capabilities in a competitive market.
When we talk about optimizing efficiency in direct-to-film printing, it’s vital to understand that various methods and tools come into play. The term ‘direct to film’ captures a process that allows for high-quality design transfers onto a wide range of substrates. Achieving optimal results in this domain involves embracing cutting-edge technology and implementing the most effective practices. By focusing on aspects such as quality equipment and innovative inks, businesses can streamline their DTF workflows significantly. This comprehensive overview will provide insights on how to leverage these various elements to realize full operational potential and superior print quality.
Enhancing DTF Printing Efficiency: Key Considerations
To harness the full potential of DTF (Direct to Film) printing, it is crucial for businesses to focus on maximizing operational efficiency. This can be achieved through a variety of strategies that include investing in high-quality equipment and modernized DTF printing tools. With the right setup, companies can see significant improvements in print speed and quality, leading to reduced turnaround times and increased customer satisfaction. Additionally, incorporating LSI concepts like ‘efficient DTF processes’ and ‘best DTF printing techniques’ into operational practices will not only streamline production but also enhance the overall effectiveness of each printing job.
Moreover, training staff on the importance of these efficiencies can result in a more knowledgeable and skilled team. Awareness of how each element affects printing efficiency, from ink formulations to print settings, can lead to a more cohesive workflow. By fostering an environment where efficiency is prioritized, businesses set the stage for continuous improvement and innovation in DTF printing, allowing them to stay competitive in the evolving marketplace.
The Role of High-Quality DTF Printers
High-quality DTF printers form the backbone of a successful printing operation. Brands like Epson and Roland have established themselves as leaders in the industry, offering models that excel in both speed and resolution. Investing in these models not only enhances the quality of output but also significantly improves printing efficiency. By utilizing state-of-the-art technology that allows for high-speed production without sacrificing detail, businesses can meet client demands swiftly and effectively. The return on investment for high-quality printers can be seen in both operational throughput and customer satisfaction.
Furthermore, upgrading to advanced DTF printers can integrate seamlessly with improved inks and films, creating a holistic approach to maximizing efficiency. The synergy between quality printers and high-performance materials fosters an environment where businesses can produce stunning, durable prints without the common pitfalls of inefficiency. Ultimately, selecting the right DTF printing equipment is not just about immediate output; it’s a strategic investment in the future success of the business.
Choosing the Right Films for Improved DTF Efficiency
The choice of transfer films is a critical factor that can dramatically affect DTF printing efficiency. Opting for high-quality PET films that are specifically engineered for DTF applications can enhance ink adhesion and ensure vibrant colors. This not only leads to superior print quality but also minimizes the likelihood of reprints, thus saving both time and materials. Businesses are increasingly leaning towards eco-friendly films that meet sustainability standards, allowing them to improve their green footprint while achieving top-tier print results.
Additionally, the correct film choice can influence the heat transfer process’s effectiveness. Films that are not properly coated can result in poor transfer quality, leading to wasted resources and increased costs. By investing in premium films, businesses can ensure that every print runs smoothly and efficiently, furthering their commitment to delivering high-quality products that meet client expectations. Implementing best practices in film selection is essential for maximizing the overall DTF printing process.
Effective Techniques for Ink Management
Efficient ink management strategies are fundamental for optimizing DTF printing processes. With advancements in DTF ink formulations, businesses can achieve better coverage with reduced ink consumption. This not only cuts down costs significantly but also aligns with eco-friendly practices, an increasingly important consideration for consumers today. By selecting ink suppliers that prioritize innovation, companies can leverage the latest developments to enhance both their profit margins and environmental responsibility.
In addition, monitoring ink usage can provide valuable insights into the efficiency of the printing operation. Regular audits of ink consumption can help identify any discrepancies or issues that may lead to excess wastage. Using tools designed for accurate ink management can aid printing companies in maintaining consistent quality while optimizing their usage, ultimately driving down costs. This strategic oversight of ink resources is a vital component of improving the efficiency of the DTF printing process.
Streamlining Pre-press Procedures for Efficiency
Optimizing pre-press procedures is crucial for enhancing DTF printing efficiency. By implementing comprehensive checks and thorough color profiling, businesses can substantially reduce the occurrence of errors that lead to reprints. Techniques such as correctly setting print parameters before the production process begins ensure that each print is executed flawlessly. Continuous education and training of staff on effective pre-press strategies can cultivate a culture of precision and quality, resulting in increased output and reduced waste.
Moreover, utilizing advanced software for pre-press preparations can further enhance workflow efficiency. Software solutions that offer predictive analytics and layout optimizations minimize the margin for error while maximizing printable areas, hence reducing paper and ink waste. Keeping the team updated on the latest pre-press technologies and techniques through professional development opportunities can empower them to produce superior results consistently. In essence, a well-structured pre-press workflow lays the foundation for successful DTF printing.
Innovating Post-Processing Techniques for Better Results
Post-processing techniques play an integral role in ensuring high-quality results in DTF printing. Advanced curing technologies that incorporate precise temperature controls can enhance print durability while speeding up the curing phase. This step is vital as it determines the longevity and quality of the prints produced. By investing in cutting-edge post-processing equipment, businesses can ensure that they are not only meeting client expectations but exceeding them with superior product offerings.
Additionally, businesses are encouraged to stay abreast of innovations that can accelerate drying processes without compromising quality. Solutions such as infrared drying or heated conveyor networks can significantly enhance production speed while maintaining the integrity of the print. Streamlined post-processing not only improves operational efficiency but also contributes to an overall reduction in turnaround times, a critical factor in maintaining competitive advantage in the DTF printing market.
Frequently Asked Questions
What are the best DTF printing techniques to improve DTF printing efficiency?
To improve DTF printing efficiency, focus on optimizing pre-press and post-printing processes. Techniques like color profiling, proper film selection, and efficient ink usage greatly enhance the outcome. Also, invest in high-quality DTF printers for better throughput and resolution.
How do high-quality DTF printers impact printing efficiency?
High-quality DTF printers boost printing efficiency by enabling faster print speeds and producing higher resolution outputs. Brands like Epson and Roland have technology that minimizes downtime, leading to better overall productivity and reduced costs.
What role do DTF printing tools play in achieving efficient DTF processes?
DTF printing tools, including advanced heat presses and software for color management, are essential for achieving efficient DTF processes. They help streamline operations, minimize ink waste, and ensure consistent print quality.
How can I choose proper films to maximize DTF printing efficiency?
To maximize DTF printing efficiency, choose high-quality PET films with coated surfaces designed for better ink adhesion. These films improve transfer quality and durability while reducing the likelihood of print errors.
How can training staff improve DTF printing efficiency?
Training staff on best practices and operational techniques directly contributes to DTF printing efficiency. Well-trained employees can execute maintenance schedules, optimize print settings, and reduce reprints, all of which are vital for maintaining high output quality.
What maintenance practices are crucial for high DTF printing efficiency?
Regular maintenance practices, such as cleaning print heads and calibrating equipment, are crucial for high DTF printing efficiency. A solid maintenance schedule ensures optimal performance of high-quality DTF printers, ultimately enhancing print outcomes and reducing downtime.
Key Points | Details |
---|---|
Introduction | Maximizing DTF printing efficiency is essential for productivity and quality. |
Understanding DTF Printing | DTF printing uses film and heat to transfer designs onto fabrics. |
1. High-Quality Printers | Invest in reliable brands like Epson or Roland for better output quality. |
2. Choosing Proper Films | Select high-quality, eco-friendly PET films for better ink adhesion. |
3. Optimizing Ink Usage | Use innovative DTF inks for improved coverage and reduced waste. |
4. Effective Pre-press Procedures | Thorough checks minimize reprints and enhance workflow efficiency. |
5. Post-Processing Improvements | Advanced curing technology enhances durability and speed. |
6. Software Enhancements | Utilize updated software for layout and ink management efficiencies. |
7. Maintenance and Training | Regular maintenance and ongoing staff training ensure optimal performance. |
Summary
DTF printing efficiency is crucial for businesses looking to maintain a competitive edge while delivering high-quality prints. Achieving this efficiency requires a comprehensive strategy, which includes investing in top-tier equipment, selecting the right materials, and prioritizing staff training. By focusing on these key areas, businesses can enhance productivity, minimize waste, and ensure that every print meets the highest standards. Continuous improvements and innovations in technology will further bolster the effectiveness of DTF printing operations, paving the way for sustained success in the industry.