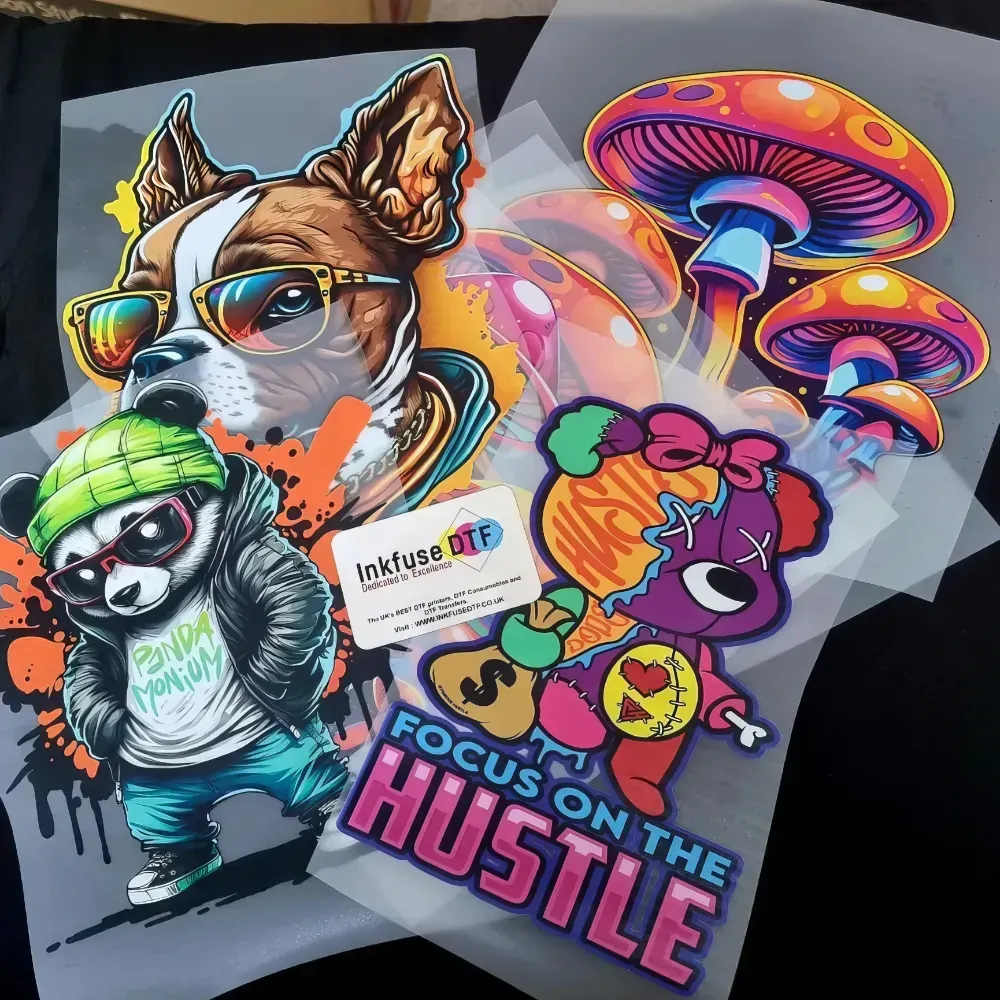
DTF transfers, or Direct to Film transfers, are revolutionizing the garment printing industry by offering a versatile and high-quality method for customizing apparel. This innovative printing technique utilizes specially designed films and vibrant inks to deliver striking designs that adhere well to various fabric types, including cotton and polyester. Whether you are a business owner eager to dive into custom apparel printing or a DIY enthusiast looking for the latest garment printing techniques, understanding DTF transfers is essential for ensuring successful projects. With the advantages of long-lasting prints and cost-effective setups, DTF printing equipment is becoming increasingly popular among entrepreneurs seeking to make their mark in the apparel market. By embracing DTF transfers, you open the door to endless possibilities in personalized fashion.
Direct to Film printing, often referred to as DTF, has emerged as a transformative approach in the realm of textile decoration. This cutting-edge method combines advanced technology with practical applications, catering to both large-scale apparel manufacturers and small business owners who specialize in custom apparel printing. DTF enables creators to produce stunning, high-resolution graphics that maintain their vibrancy over time, making it a favored choice among garment printing techniques. The process simplifies the creation of diverse designs while reducing the complexity often associated with traditional methods. In this evolving landscape of garment customization, embracing DTF printing advantages can significantly enhance one’s offerings, leading to a more dynamic and responsive apparel business.
Understanding the Basics of DTF Transfers
DTF Transfers, or Direct to Film transfers, revolutionize garment printing by employing an ingenious method that prints stunning graphics onto a specialized film. Through a tailored inkjet printer, vibrant inks are printed, ensuring compatibility with the film used, which is equally critical for achieving the necessary quality. The process involves coating the printed film with hot-melt adhesive powder, allowing users to transfer striking designs onto various fabrics, including cotton, polyester, and mixed blends. This versatility makes DTF printing suitable for any custom apparel project.
When compared to other garment printing techniques, DTF transfers stand out primarily due to their ability to work on multiple substrates without compromising quality. Traditional methods like screen printing often have limitations based on the type of fabric and design complexity, whereas DTF allows for more creativity in artwork dimensions and fabric types. By understanding the fundamentals of DTF printing, businesses can tap into a lucrative segment of the market that craves personalized and high-quality clothing options.
Exploring the Advantages of DTF Printing
The advantages of DTF printing are multifaceted, making it highly appealing to both small business owners and larger manufacturers. One notable benefit is the exceptional color vibrancy achieved with specialized inks, leading to prints that stay bright and true, even after numerous washes. This durability is essential for maintaining the quality that customers expect from customized clothing. DTF prints not only boast aesthetic appeal but also significant longevity, affirming their reputation as a top choice in garment printing.
Furthermore, DTF printing is recognized for its cost-effectiveness, especially for those entering the custom apparel market. Initial investment in DTF equipment and materials is often lower compared to traditional screen printing setups that require extensive plant and machinery. This especially strikes a chord with entrepreneurs who might be on a limited budget but wish to deliver high-quality prints. Ultimately, DTF transfers offer a perfect balance of quality, versatility, and affordability, making them a strategic choice for budding businesses.
Essential Equipment for DTF Printing
To reap the full benefits of DTF transfers, certain specialized equipment is vital. A dedicated DTF printer specifically designed to handle the unique ink and film is the cornerstone of any DTF operation. This provides exceptional print quality and reliability, minimizing issues like clogs or color mismatches. Additionally, acquiring high-quality transfer films and hot-melt adhesive powder is crucial to ensure that each print adheres effectively and retains its vibrant appearance over time.
A heat press is also an indispensable piece of equipment for successful DTF printing. This tool ensures that the printed design transfers to the garment securely and evenly, preventing common issues such as bubbling or peeling. Coupled with graphic design software, which facilitates the creation and customization of designs, this arsenal of equipment allows businesses to execute their projects with precision, setting the stage for pristine finished products that stand out in a competitive market.
Mastering the DTF Printing Process
The DTF printing process is straightforward yet demands attention to detail for the best outcomes. It begins with design creation, where you can utilize graphic design software to bring your ideas to life. Once your artwork is primed, it is printed onto the DTF film using a DTF printer, leading to the vibrant imagery that customers will expect. After printing, the critical step of applying adhesive powder ensures the design adheres perfectly to the fabric, setting the foundation for a quality transfer.
The next phase involves the heat transfer process, where the printed film is carefully applied to the garment using a heat press. This step requires optimal pressure and temperature to guarantee a smooth transfer without blemishes. Understanding each stage of this comprehensive process is essential for mitigating risks associated with peeling or fading of the prints. With practice and fine-tuning, businesses can master DTF printing, resulting in high-caliber products that excite and satisfy customers.
Current Trends in DTF Printing
As the DTF printing market expands, several key trends have emerged, reshaping how entrepreneurs approach garment customization. Increasing demand for personalized apparel solutions has propelled small business owners to consider DTF as a feasible option due to its broad adaptability and efficiency. Technological advancements enhance not only the printing speed but also color accuracy, making DTF printing a coveted choice among industry players looking to maintain a competitive edge.
Alongside the growth in technology, there exists a burgeoning community of DTF enthusiasts, with numerous online forums dedicated to sharing tips and experiences. These resources provide invaluable support for newcomers, allowing them to navigate the intricacies of DTF printing with confidence. The combination of technological evolution and community collaboration is forecasted to propel DTF transfers further into mainstream apparel customization, solidifying its position as a staple in the garment printing industry.
Navigating the Challenges of DTF Printing
While the benefits of DTF printing are vast, it is imperative to be aware of potential challenges. Initial setup costs, though lower than traditional printing methods, can still represent a significant investment, especially when purchasing quality equipment. For startups, ensuring your initial outlay aligns with your long-term business goals is essential to avoid financial strain during the early stages.
Additionally, the DTF printing process has a learning curve that cannot be overlooked. Mastering the practical aspects of applying DTF transfers, such as adjusting temperatures and pressures for various fabrics, is crucial. New users often face pitfalls, such as improper adhesion or fading prints, if they do not invest time in mastering the technique. However, once these challenges are navigated, the potential for success and creativity is tremendous.
Frequently Asked Questions
What are DTF transfers and how do they work?
DTF transfers, or Direct to Film transfers, involve printing images onto a specialized film that is then heat-pressed onto fabric. This method uses a modified inkjet printer and hot-melt adhesive powder for strong adhesion to various materials like cotton and polyester, resulting in vibrant and durable prints.
What are the advantages of using DTF printing over other garment printing techniques?
DTF printing boasts several advantages, including versatility across fabric types, vibrant color output, and cost-effectiveness. Unlike traditional methods that may be limited by fabric, DTF transfers can adhere to various materials, making them ideal for custom apparel businesses.
What equipment is required for DTF printing?
Essential DTF printing equipment includes a specialized DTF printer, high-quality transfer film, adhesive powder, a heat press, and graphic design software. This combination ensures that you can efficiently create and apply vivid designs to garments.
How does the DTF printing process work?
The DTF printing process involves several steps: creating a design in graphic design software, printing it onto DTF film with a DTF printer, applying adhesive powder, and then heat pressing the design onto the garment. Following these steps ensures effective and attractive prints.
What should I consider when venturing into DTF printing?
When starting with DTF transfers, consider the initial setup costs, the learning curve associated with mastering the printing process, and the importance of using quality materials. Ensuring proper maintenance of your equipment is also crucial for optimal results.
What are some best practices for successful DTF printing?
To achieve the best results with DTF transfers, use high-quality materials, maintain your printer regularly, and be willing to experiment with different settings. These practices will help optimize the printing process and enhance the durability and appearance of your prints.
Key Point | Description |
---|---|
What Are DTF Transfers? | A method using special film and heat for printing images on fabric with vibrant results. |
Advantages of DTF Printing | Versatile prints on various fabrics, vibrant colors, and a cost-effective option for small businesses. |
Essential Equipment | DTF Printer, Transfer Film, Adhesive Powder, Heat Press, Graphic Design Software. |
DTF Printing Process | Involves design creation, printing on film, applying adhesive powder, and heat transferring to fabric. |
Current Market Trends | Growth driven by technology, appealing to small businesses in customizable apparel. |
Challenges in DTF Printing | Initial setup costs and a learning curve for new users can hinder success. |
Best Practices | Use quality materials, maintain equipment, and experiment with settings for optimal results. |
Summary
DTF Transfers are rapidly reshaping the garment printing landscape, utilizing a uniquely effective method that combines vibrant colors with durability. As a versatile printing solution, DTF transfers allow for customization across various fabric types, appealing to a wide array of users from small business owners to DIY enthusiasts. With the requisite investment in specific equipment and adherence to best practices, practitioners in the industry can fully exploit the potential of DTF printing, ensuring high-quality outcomes that resonate with consumers. The emerging trends in the DTF market, paired with ongoing technological advancements, promise continued growth and opportunity for those looking to enter the customizable apparel niche.