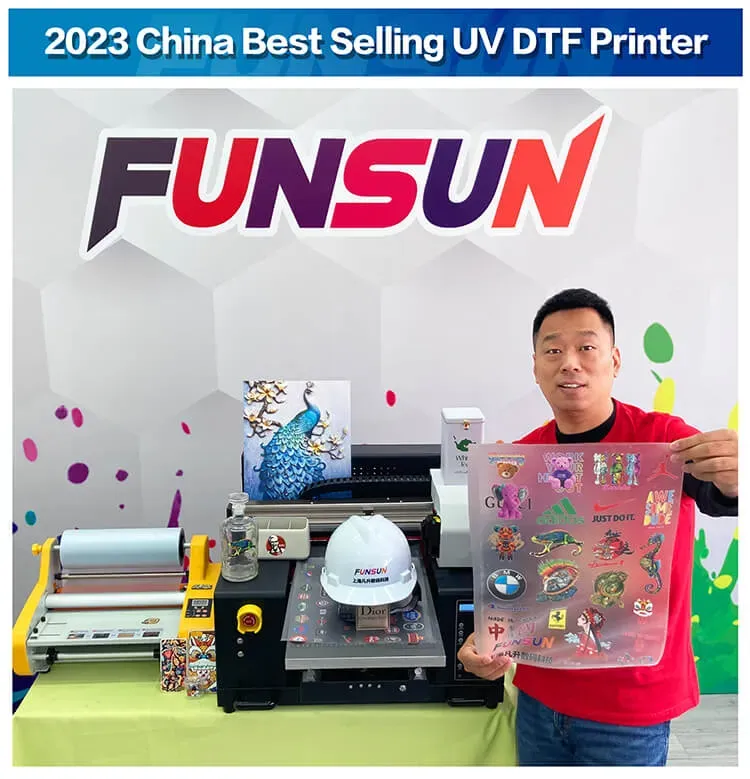
UV DTF printing, or ultraviolet direct to film printing, is revolutionizing the printing industry with its ability to create vibrant and durable images on a variety of surfaces. This innovative printing technology employs UV light to instantly cure ink, resulting in stunning prints that maintain their brilliance over time. As you delve into mastering UV DTF printing, you will discover that understanding the nuances of UV printing techniques is essential for achieving professional results. From selecting the right UV DTF printing materials to exploring effective tips for UV DTF printing, this guide will provide you with the insights needed to elevate your projects. Join us as we explore the essential elements and techniques involved in harnessing the full potential of UV DTF printing for your creative endeavors.
When discussing modern printing methods, ultraviolet direct-to-film (DTF) printing has emerged as a cutting-edge approach that seamlessly combines creativity and technology. Known for its ability to deliver exceptional color vibrancy and durability, this technique allows users to print on a broad range of substrates, making it a favored choice in many industries. By understanding alternative terms and related concepts, such as UV printing technology and DTF transfer techniques, you can broaden your comprehension of the printing landscape. Whether you are a professional looking to refine your craft or a beginner exploring new avenues, grasping the fundamentals of this advanced printing process is vital. Let’s dive deeper into the world of UV DTF printing and unlock a realm of creative possibilities.
All You Need to Know About UV DTF Printing Materials
In the realm of UV DTF printing, choosing the right materials is crucial for achieving stunning results. UV DTF printing is versatile and allows you to print on various substrates, including plastics, fabric, wood, and metals. Each material has unique properties that affect the ink’s adhesion and overall print quality. For instance, porous materials like cotton absorb UV inks differently than non-porous surfaces like acrylic or glass. Understanding these characteristics will enable you to select the appropriate substrate for your projects, ensuring vibrant and durable results.
Additionally, the compatibility of the chosen materials with UV inks plays a significant role in the overall success of your printing projects. Not all materials are equally receptive to UV DTF printing. Factors such as surface texture, finish, and preparation techniques can influence the results. Before embarking on a new project, conduct thorough research and testing to determine how various materials will interact with your specific inks and printing techniques, leading to more effective and creative outcomes.
Essential Tips for Successful UV DTF Printing Projects
Successfully executing UV DTF printing projects requires a careful blend of technical understanding and creative design. One of the most valuable tips is to always conduct test prints before finalizing any large job. Test prints allow you to gauge how your designs translate onto different materials and help you make necessary adjustments to color settings and curing techniques. This step is particularly important when incorporating complex graphics or vibrant colors, as test samples can reveal potential issues early on and save both materials and time.
Another critical tip is to keep all aspects of your print project well-organized, from design files to print settings. Ensuring that your files are correctly formatted and set up with appropriate color profiles can drastically improve the quality of your prints. Make sure the resolution is high enough to produce clear, professional-looking results. By blending organizational strategies with creative experimentation, you can elevate your UV DTF printing projects to achieve outstanding visual results.
Mastering the Calibration of Your UV DTF Printer
Proper calibration of your UV DTF printer is one of the most essential steps to ensure top-quality printing results. Calibration involves fine-tuning the printer’s settings, including the print head alignment and the distance between the print heads and the material surface. Taking the time to calibrate your equipment minimizes common printing issues like banding, color inconsistency, and misalignment, which can spoil an otherwise perfect print. Familiarize yourself with the manufacturer’s guidelines and perform regular checks to maintain optimal printer performance.
You should also consider environmental factors that could affect calibration. Factors such as humidity and temperature can influence the adhesion and curing of UV inks, thus impacting the overall print quality. By monitoring these conditions and adjusting your printer settings accordingly, you can ensure a consistent output across different projects and materials. Mastering calibration is a continuous learning journey, but with diligence, you will see a marked improvement in the quality of your prints.
Exploring Different Curing Techniques in UV DTF Printing
Curing is a pivotal step in the UV DTF printing process that significantly impacts the final product’s quality and durability. The curing process involves using ultraviolet light to harden the printed ink, ensuring it adheres strongly to the chosen substrate. There are various curing techniques employed in the UV DTF printing process, including traditional UV curing and modern UV LED curing. Each method has specific advantages and is suited for different applications. For example, UV LED curing is often preferred for its energy efficiency and lower heat output, making it ideal for heat-sensitive materials.
Experimenting with different curing techniques and understanding their effects on various inks and substrates can lead to better project outcomes. It is essential to explore various curing times and settings to discover the combination that yields the best results for your specific projects. By mastering the curing process, you can achieve vibrant colors, heightened durability, and professional finishes that set your work apart from the competition.
Tips for Effective Design Preparations in UV DTF Printing
When preparing designs for UV DTF printing, there are several crucial aspects that you must consider to ensure optimal print results. Firstly, always work with high-resolution files. A resolution of at least 300 DPI is recommended to achieve clarity and sharpness in your prints. Additionally, it’s essential to create designs that are tailored to the characteristics of the specific substrate you’ll be using. For example, a design intended for use on a glossy surface may require adjustments compared to one meant for a textured or matte finish.
Furthermore, pay close attention to the color settings in your design files. Colors might appear differently on-screen than they do when printed due to variations in monitor displays and printing processes. Using color management software can help align your digital designs with the actual output you are aiming for, ensuring that your colors are consistent and true to your vision. By taking these design preparation tips into account, you can significantly enhance the quality of your UV DTF printing projects.
Staying Ahead with Innovations in UV DTF Printing
The UV DTF printing industry is evolving rapidly, with advancements in technology leading to innovative practices that can enhance your printing projects. Staying informed about these developments is vital for anyone aiming to master UV DTF printing effectively. New printer models, improved UV inks, and novel curing technologies are continually being introduced to the market, offering new possibilities for creative expression and production efficiency. Engaging with industry forums, attending seminars, and following pertinent publications can keep you updated on the latest trends and techniques.
Moreover, participating in the printing community allows for shared experiences and insights, which can catalyze your learning curve in UV DTF printing. Networking with fellow printers can provide opportunities to exchange tips, discuss troubleshooting methods, and explore unique project ideas. Staying connected with technological advancements in the printing field not only enhances your skills but also empowers your projects with cutting-edge tools and methods that set you apart from competitors.
Frequently Asked Questions
What are the key advantages of UV DTF printing over traditional printing methods?
UV DTF printing offers several advantages, such as the ability to print on a diverse range of materials like plastic, wood, and metal, which traditional methods often limit. Additionally, UV DTF printing provides vibrant colors and durable prints that are resistant to fading and scratches, thanks to the immediate curing process that UV light facilitates.
What materials are best suited for UV DTF printing?
When mastering UV DTF printing, it’s essential to know that materials such as non-porous surfaces like plastics and metals yield the best results. However, porous materials like canvas can also be used effectively. Understanding the properties of your chosen UV DTF printing materials will influence your ink selection, curing times, and print settings for optimal output.
How can I ensure my UV DTF printing projects have high clarity and precision?
To guarantee high clarity and precision in UV DTF printing projects, always design at a high resolution (at least 300 DPI) and conduct test prints on the same substrate as your final piece. Proper calibration of your printer and understanding the print settings required for glossy or matte finishes will further enhance the quality of your prints.
What maintenance practices are essential for UV DTF printing equipment?
To maintain UV DTF printing equipment and ensure consistent quality, regularly clean the print heads, replace any worn components, and check that UV lights are functioning correctly. Implementing a comprehensive maintenance routine significantly prolongs the lifespan of your printer and improves the overall quality of your printed projects.
What ink types should I consider for UV DTF printing projects?
In UV DTF printing, it’s crucial to understand the different ink types available. Common choices include solvent-based, water-based, and UV-curable inks, each with unique properties and durability levels. Selecting the right ink type based on your specific project requirements is vital for achieving the desired results and ensuring adhesion and vibrancy on your chosen materials.
How do curing techniques impact the outcome of UV DTF printing?
Curing techniques play a vital role in UV DTF printing, as they harden the ink and ensure it firmly adheres to the substrate. Different methods, such as UV LED curing, can affect the vibrancy and durability of your prints. Experimenting with various curing times and techniques is essential to determine the best combination for your specific materials and inks.
Tip Number | Key Point |
---|---|
1 | Know your materials for optimal ink adhesion. |
2 | Ensure printer calibration for consistent results. |
3 | Design with the print settings in mind to achieve clarity. |
4 | Conduct test prints to avoid material waste. |
5 | Prepare design files carefully, accounting for color profiles. |
6 | Maintain equipment for longevity and quality output. |
7 | Understand different ink types for specific applications. |
8 | Experiment with curing techniques for durability. |
9 | Stay updated on the latest technology trends. |
10 | Engage with community resources for support and ideas. |
Summary
UV DTF printing represents a cutting-edge transformation in the printing landscape, allowing for vibrant and durable prints on a plethora of substrates. Whether you’re just beginning or looking to enhance your expertise, following the ten essential tips outlined above will equip you with the knowledge and skills necessary for success. By understanding materials, calibrating printers, and exploring your community, you can optimize your printing results and expand your creative horizons. Embrace the possibilities of UV DTF printing and unlock the potential of your projects.