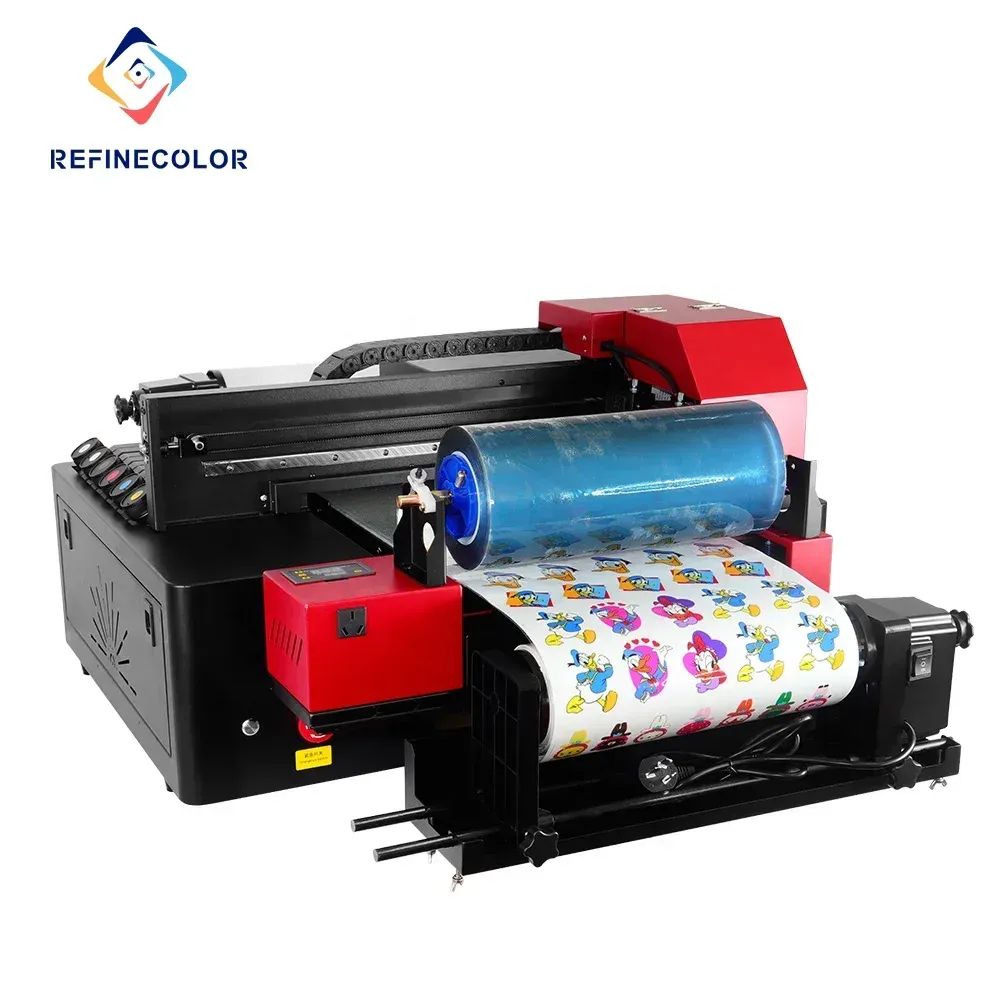
UV DTF (Ultra Violet Direct to Film) printing has rapidly revolutionized the printing landscape, offering vivid, durable designs across a multitude of substrates. This innovative technique harnesses the power of advanced UV inks to bring images to life in ways traditional printing methods often cannot achieve. With UV DTF, businesses can create stunning custom apparel and promotional items that truly stand out. Navigating through the intricacies of UV DTF printing is essential for optimizing your results and enhancing customer satisfaction. In this article, we will delve into best practices for UV DTF, providing valuable tips and strategies to maximize your printing potential.
Exploring the realm of UV Direct to Film printing opens up a wealth of opportunities for high-quality graphic reproductions. Often referred to as ultraviolet DTF printing, this method is essential for anyone looking to produce sharp and resilient images on various materials. The cutting-edge technology not only optimizes the application of inks but also guarantees faster curing times, setting it apart from conventional techniques. As we examine the key elements for successful printing with this innovative process, you’ll discover effective ways to enhance your results and ensure that your products meet industry standards. Whether you’re new to this technique or seeking to refine your skills, understanding these nuances is crucial for thriving in today’s competitive market.
Understanding UV DTF Printing Technology
UV Direct to Film (DTF) printing is revolutionizing how we think about custom printing. Unlike traditional methods, the UV DTF process utilizes ultraviolet light to cure inks directly onto transfer films, which are then transferred to various substrates. This method is not only faster but also provides stunningly vibrant and durable prints. The technology allows for a wide range of applications across multiple materials, including textiles, plastics, and even wood, making it an incredibly versatile choice for businesses seeking quality and efficiency.
The unique combination of UV curing and high-quality inks in UV DTF printing allows for finer details and richer colors compared to other printing techniques. The curing process ensures that inks dry almost instantaneously, preventing smudging and ensuring that the end product retains its integrity even under challenging conditions. The ability to print detailed images and text on diverse surfaces sets UV DTF apart as a preferred choice for custom apparel and promotional items.
Best Practices for UV DTF Success
To maximize the quality of your UV DTF prints, following established best practices is crucial. First and foremost is the printer calibration process; it’s essential to adjust ink density, print speed, and temperature settings specific to the material being printed on. A well-calibrated printer minimizes color bleeding and enhances adhesion, resulting in a more professional-looking final product.
Another vital best practice is to select high-quality transfer films that are designed explicitly for UV applications. These specialty films often include coatings that provide excellent ink absorption and improve adhesion to different substrates. By prioritizing quality in both your printer setup and material selection, you can ensure vibrant, long-lasting prints that meet or exceed customer expectations.
Optimizing UV DTF Results for Client Satisfaction
Achieving optimal results in UV DTF printing is a multifaceted process that can greatly enhance client satisfaction. One of the key components involves selecting the right inks that are UV-resistant and compatible with your printer’s specifications. High-quality inks yield brighter colors and improve durability, critical for final products like apparel that face wear and tear.
Additionally, employing effective surface preparation techniques before printing significantly impacts the adhesion and overall quality of the print. Cleaning the substrate thoroughly is vital to prevent defects and ensure a smooth, professional finish. This attention to detail not only enhances the aesthetics of the print but also fosters greater customer trust and satisfaction.
Tips for Proper Surface Preparation
Surface preparation is a crucial step in the UV DTF printing process that can greatly influence print quality. The substrate must be free of dust, grease, and other contaminants before printing. Using isopropyl alcohol for cleaning can achieve a clean surface ideal for ink adhesion, leading to smoother prints and longer-lasting results.
Moreover, understanding the unique characteristics of different substrates is essential. Some materials may require specific pre-treatment processes, while others might benefit from roughening the surface to enhance ink adhesion. Familiarizing yourself with these nuances will allow you to tailor your surface preparation methods, ensuring optimal outcomes for every project.
Perfecting the Curing Process in UV DTF
The curing process in UV DTF printing is critical to achieving quality and durability in the final print. Proper exposure to UV light is essential, as insufficient curing can lead to smudging or fading of the print over time. Utilizing the right UV curing equipment and understanding the exposure times for different substrates can dramatically improve the consistency and longevity of your prints.
To perfect the curing process, it is beneficial to conduct thorough tests with various substrates and curing lamp configurations. This experimentation will help you understand how different materials react to UV exposure, allowing you to set the ideal parameters for each type. Ensuring uniform exposure across all areas of the print can be the difference between a subpar result and a striking, professional-grade finish.
Maintaining Your UV DTF Printer for Longevity
Routine maintenance is essential for keeping your UV DTF printer functioning optimally. Regularly cleaning the print heads and monitoring ink levels can help prevent common printing issues that could compromise print quality. Following the manufacturer’s recommendations for maintenance schedules ensures your printer remains in peak condition, minimizing unexpected downtime.
Additionally, performing periodic diagnostics can identify potential issues before they escalate into more significant problems. Consistent maintenance not only extends the lifespan of your equipment but also guarantees that you can deliver high-quality prints consistently, thus maintaining customer loyalty and satisfaction.
Frequently Asked Questions
What is UV DTF printing and how does it work?
UV DTF printing, or UV Direct to Film printing, uses advanced UV inks to transfer vibrant images onto various substrates. It employs ultraviolet light to cure the inks quickly, resulting in high-quality, durable prints suitable for textiles, plastics, wood, and more.
What are some essential best practices for UV DTF printing?
To achieve the best results in UV DTF printing, calibrate your printer correctly, select high-quality transfer films, choose durable UV-resistant inks, prepare surfaces thoroughly, and master the curing process. Following these best practices will enhance print quality and longevity.
How can I optimize UV DTF results for different substrates?
Optimizing UV DTF results involves adjusting printer settings based on the substrate type, using appropriate inks, ensuring the surface is clean for adhesion, and testing different curing times. Experimentation with various materials will also help you fine-tune your approach.
What tips can improve the curing process in UV DTF printing?
To improve the curing process in UV DTF printing, use appropriate UV curing lamps that provide sufficient exposure to all areas of the print. It’s important to test different curing times for various substrates to achieve the best durability and quality.
What role does surface preparation play in UV DTF printing?
Surface preparation is critical in UV DTF printing. Ensuring that the substrate is clean and free from contaminants enhances ink adhesion and prevents issues such as smudging or peeling. Clean surfaces with suitable agents like isopropyl alcohol for optimal results.
How often should I perform maintenance on my UV DTF printer?
Routine maintenance is essential for the longevity of your UV DTF printer. Regular cleaning of print heads, checking ink supplies, and conducting diagnostics as per the manufacturer’s guidelines will ensure consistent quality output and minimize potential issues.
Aspect | Details |
---|---|
Definition | UV Direct to Film (DTF) printing uses UV inks to create durable, vibrant prints on diverse substrates. |
Process | Transfers high-quality images using UV light, allowing for fast drying and strong adhesion. |
Calibration | Proper printer settings (ink density, speed, temperature) are critical to prevent issues. |
Film Selection | High-quality UV transfer films enhance print durability and appearance. |
Ink Quality | Using UV-resistant inks improves color vibrancy and print lifespan. |
Surface Preparation | Clean surfaces are essential for optimal adhesion and print quality. |
Curing Techniques | Proper UV curing is crucial for durability; test exposure times. |
Layering | Allow drying time between layers to prevent smudging and ensure adherence. |
Testing | Conduct test prints to refine settings and materials for better results. |
Maintenance | Regular upkeep ensures the printer functions properly and consistently. |
Summary
UV DTF printing is a groundbreaking technique that transforms the way we think about custom printing, offering exceptional quality and durability in prints across various substrates. By understanding the fundamentals of this process, including printer calibration, ink selection, and surface preparation, businesses can significantly enhance their production quality and efficiency. This guide provides valuable insights into mastering UV DTF printing, ensuring that you are equipped with the knowledge to achieve stunning results that meet and exceed customer expectations. With ongoing practice and experimentation, your capabilities in UV DTF printing can evolve, paving the way for creativity and innovation in your projects.